When it comes to dental equipment maintenance, there are a few key things to keep in mind. Proper maintenance of dental equipment not only improves the durability and longevity of your investment but also helps you avoid costly repairs that can be expensive for both you and your practice.
Regular preventive care is an important part of maintaining any piece of medical or surgical equipment. The same goes with maintaining dental equipment; regular cleaning will help extend its life and ensure optimal performance.
In this post we’ll take a look at some common issues dentists face when it comes to their maintaining their equipment and how they can prevent them from happening. Before going any further, it’s always a good reminder to keep the manufacturer’s instruction manual for cleaning and caring for your equipment.
It usually contains information that is specific to the product in question, which if not carefully followed, your efforts to upkeep the equipment may result in more harm than good. As best as you can, try to avoid generic tools when maintaining the equipment. Stick to manufacturer approved tools because there might be a perfectly good reason that you are not yet aware of. Failure to do so could risk damaging the equipment and even void the product warranty.
With that out of the way, this equipment maintenance guide explores some of some important aspects of maintaining your prized dental gear.
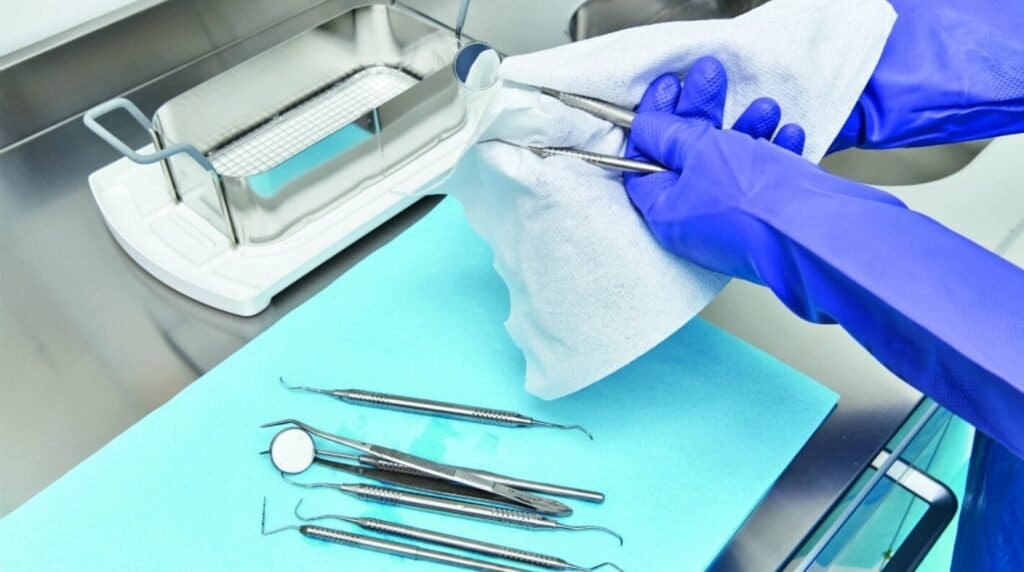
Types of dental equipment maintenance
There are many different ways of keeping your dental fixtures or instruments in good shape. Some methods require professional help while most just require basic duties that a dental assistant can accomplish.
Here is a list of common types of dental tool and equipment maintenance tasks:
Preventive Maintenance
Dental equipment preventative maintenance is usually done once every few months by cleaning and lubricating all moving parts on the equipment. It also includes checking for leaks and cracks and replacing worn components as needed. The most common preventive maintenance tasks include oiling and greasing moving parts such as motors, gears, bearings, etc.
In addition to these basic procedures, you may need to replace seals that have been damaged due to wear over time. Also check the fluid level in hydraulic cylinders. If it’s low, add more oil. You’ll find instructions with each piece of apparatus about how often this should be performed.
Cleaning
This can involve washing down surfaces like handles or knobs so they don’t get sticky from food particles or bacteria build up. It also involves cleaning out reservoirs where fluids are stored for use during a procedure. The reservoir will likely contain some type of filter system that needs to be cleaned periodically. In addition, you may need to clean and lubricate moving parts such as motors or gears.
Disinfection
In the age of COVID-19, dental surgeries need to devote more time and effort to tighten up infection control measures. Disinfection is one of the cornerstones that required daily attention.
If your practice has an in-office sterilization unit, it’s important to disinfect all items before each patient visit. This includes handpieces, air compressors, drills, scalers, suction tips, ultrasonic instruments, etc. It also means cleaning any surfaces where patients touch them with their hands prior to treatment.
Dental Autoclave
It goes without saying that the dental autoclave is your first port of call when it comes to cleaning and disinfecting your handheld instruments.
While the dental autoclave, also known as a steam sterilizer, should be a necessary part of your sterilization protocol to combat bacteria and debris, many dentists still neglect the following: follow the instrument care and service guidelines for their equipment; use industry-grade quality instruments; follow protocols for proper handling and packaging of sterilized instruments; and/or don’t have an effective way to monitor and maintain them in between uses.

Ultrasonic bath
One of the most effective ways to disinfect all types of instruments is by placing them into an ultrasonic bath. An ultrasound machine has been used for years to treat water and other liquids.
Ultrasound works on many different principles but basically it uses high frequency sound waves to break down organic matter like viruses, bacteria, mould spores, etc. This process can take place at room temperature so there is no heat involved which makes this method safe for patients.
Ozonated Water
Another method involves the use of an Ozonated Water Disinfection System. The system takes advantage of current electrolysis technology to dispense high grade Electrolytic Ozonated Water.
The highly reactive characteristics of ozone when dissolved in water unleashes a bacterial disinfection mechanism that breaks down cell walls of microorganisms, viruses and spike proteins – disinfecting most types of parasitic infection in seconds.
It’s as easy as dipping a cloth in the oxonated water and giving your apparatus a wipe down to prevent surface contamination. This provides a convenient way to disinfect without having to worry about cross contamination from any outside source. It can even be fitted into the flow of the dental unit water lines to purge months or years of accumulated bio films – possibly the highest source of contaminants in your practice that are infamously hard to clean.
UV light source
The UV-C rays emitted by this device kill bacteria on contact; it is also effective against viruses such as HIV and Hepatitis B & C. In a dental practice, the use of UV-C products reduces bacterial growth on surfaces and prevents cross infection between patients.
The germicidal effect lasts up to 30 minutes after exposure to the light has ended, so there’s no need for frequent cleaning. It can be used with any type of handpiece including high speed drills and sonic devices. A single treatment will disinfect all areas within reach of the wand tip, which includes most workstations, instruments and patient mouthpieces.
The output wavelength for UVC radiation falls between 200 nm and 280nm with peak effectiveness at 254nm. A typical lamp has an emission spectrum peaking around 250–270 nanometers.
This means that most of the energy will fall within a single band, which makes it easier to control than broad-spectrum lamps like halogen lights. However, because there is no visible component, these devices must be used carefully when working near patients.
Storage
When choosing a storage location, the rule of thumb is to avoid storing them in direct sunlight as it can cause damage from UV exposure.
Most manufacturers recommend storing all instruments or supplies outside during daylight hours. The recommended storage temperature should not exceed 40°F ( 4°C). In addition, some materials may discolour and become brittle with prolonged exposure to light.
For this reason, many dentists store their tools in boxes inside drawers along with other items such as handpieces, drills, etc., rather than leaving them exposed on shelves or tables.
Some newer models of electric motors have been designed to withstand the effects of heat and cold better than older designs. However, it is still important that they be stored properly so they do not get damaged by excessive temperatures.
Inspection
It’s always good practice to check for cracks or damage before using any dental equipment or instrument as that will help prevent costly repairs later on. If you notice any signs of wear, corrosion, or anything else out of place, contact your manufacturer immediately.
Dental equipment servicing personnel or technicians are trained professionals who can inspect for potential problems. They may also recommend a replacement part if necessary. For example, if the tip of an air-water syringe has been worn down and needs replacing, this could cause serious injury to patients. A technician would know how to replace such parts safely without causing harm. The same goes for other instruments like drills, scalers, etc.
Check electrical connections on all devices on a regular basis. Make sure wires aren’t frayed or loose. If any device seems faulty, replace it immediately. A simple check of an appliance’s circuit breaker panel should reveal whether anything has tripped off-line in recent months.

Repairs
Even if you have an aptitude for fixing things, dental equipment repair better left to an expert. When dental equipment breaks down, the consequences can be severe and even fatal.
Not trying to be an alarmist but when a drill overheats, it may explode with enough force that fragments will penetrate your patient’s mouth, potentially damaging their teeth and gums. You don’t want this happening on your watch!
The best way to prevent such accidents is by having regular maintenance done on all frequently used items (eg. x-ray equipment, dental chair, etc) regularly. However, regular maintenance does not guard against all types of breakdowns. In the event a breakdown in your operatory, don’t forget this golden rule: repairs should be performed by professionals who know how to safely use these tools.
Sometimes, you may be tempted to do repairs yourself because they seem simple enough or because you have no time for routine maintenance. But if something goes wrong during surgery, you could end up causing more damage than good. For example, fixing a loose wire in your handpiece can cause the motor inside it to overheat and burn out, which will lead to an even bigger problem. Applying the wrong type of lubricant on your dental drill can cause it to easily slip out of the hand while being used in an operating room. Such incidents can cause serious injury to both the patient and surgeon.
Of course, the best way to avoid breakdowns or repairs is to maintain dental equipment servicing regularly.
Calibration and certification
Although both are important aspects of quality control that should be considered when purchasing new items, they are not the same thing.
Calibrating a machine is only one part of its overall calibration process; the other half involves testing for accuracy after calibrations have been performed. Certification programs also test machines but do so by comparing their results with those of calibrated reference devices.
The manufacturer’s calibration certificate is proof that the machine has been properly calibrated before sale. A dentist who purchases his own equipment must ensure that he calibrates it regularly so as not to compromise its accuracy.
Calibrating a unit ensures that all parts are working at their optimum function, which improves efficiency and reduces downtime. It also prevents costly repairs due to faulty components or inaccurate settings. For example, regular maintenance on dental drills helps prevent overheating and allows for longer usage between restarts.
The certification is usually a mandated form of validating that the said equipment complies with the regulatory standards of the country in which it was purchased. As the owner, you have a legal responsibility to ensure that your product meets these requirements before using them.
In the case of x-ray imaging instruments, each territory has its own set of regulations that cover its ownership, use and compliance. It’s your job as the owner to make sure the service engineers and technicians performing the validation are fully accredited with the relevant bodies and that they are able to produce the relevant certification documents as mandated.
This can also be done by requesting a certificate from the manufacturer stating that they meet the relevant standard(s). Validation is typically required at the point of installation, and depending on the age of your equipment, may need to be certified periodically thereafter.
You are encouraged to request for such periodic validation, repair and service from the same authorised technician or dealer that is looking after the product.
For more information on certification and calibration, check with your product manufacturer.
Conclusion
Proper maintenance is key to keeping your surgery running smoothly and ensuring patient safety.
By following the tips in this guide, you can keep your equipment in good condition and avoid costly repairs or replacements.
Click here if you’re looking for a Dental Preventive Maintenance Checklist dividing tasks in daily, weekly, monthly and yearly actionables.
The information and viewpoints presented in the above news piece or article do not necessarily reflect the official stance or policy of Dental Resource Asia or the DRA Journal. While we strive to ensure the accuracy of our content, Dental Resource Asia (DRA) or DRA Journal cannot guarantee the constant correctness, comprehensiveness, or timeliness of all the information contained within this website or journal.
Please be aware that all product details, product specifications, and data on this website or journal may be modified without prior notice in order to enhance reliability, functionality, design, or for other reasons.
The content contributed by our bloggers or authors represents their personal opinions and is not intended to defame or discredit any religion, ethnic group, club, organisation, company, individual, or any entity or individual.
Əziz Cənab / Xanım,
Biz bu fürsətdən istifadə edərək cərrahi, stomatoloji, baytarlıq, əl alətləri və gözəllik alətlərinin ixtisaslaşmış istehsalçıları və ixracatçılarından biri olan SAADS FOUNDATION-ı təqdim etmək istərdik.
Mən sizin vebsaytınızı ziyarət edirəm və biz sizin məhsulunuzu müntəzəm olaraq hazırlayırıq;
İşlərimizi nəzərdən keçirmək üçün sizi saytımıza daxil olmağa dəvət edirik;
Veb:
https://www.saadsfoundation.com/
Seçdiyiniz alətləri bizə bildirin və keyfiyyət standartlarımızı yoxlamaq üçün hər hansı fiziki nümunələrə/sitatlara ehtiyacınız olarsa, bizimlə əlaqə saxlamaqdan çekinmeyin.
Münasib cavabınızı gözləyirik.
Hörmətlə,
More about this source textSource text required for additional translation information
Send feedback
Side panels
History
Saved
Contribute
Pervaiz Mashi
Tel : +92523550340
Tel : +923007174132
What’s app : +923416474134
Instagram: https://www.instagram.com/saadsfoundation/
Facebook: https://www.facebook.com/SaadsFoundation
Interessanter Leitfaden zum Thema Reinigung in einer Zahnarztpraxis. Oftmals habe ich in meiner Praxis keine Zeit, die Geräte selber zu säubern. Daher bin ich auch auf der Suche nach einer professionellen Reinigung.
Glad you found the article useful.
TranslatedL
Schön, dass Sie den Artikel nützlich fanden.